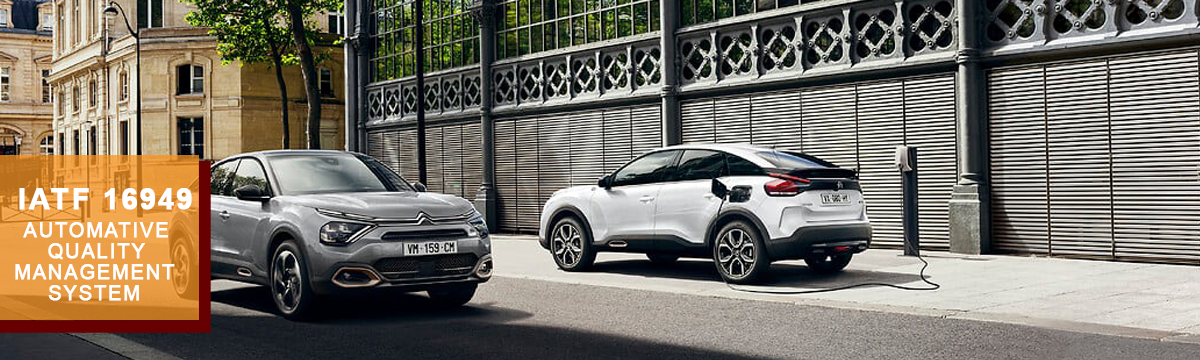
IATF 16949: Automotive Quality Management Systems
IATF 16949 is the globally recognized standard for Automotive Quality Management Systems (QMS). It helps organizations streamline their processes, maintain consistency, and continually improve performance in the automotive supply chain.
IATF 16949 is, its relationship with other ISO standards, and how it benefits companies in the automotive sector.
About the IATF 16949?
IATF 16949 is a specialized standard for the automotive industry that sets out requirements for quality management systems. It was developed by the International Automotive Task Force (IATF) and is based on the structure of the ISO 9001 standard, with additional automotive-specific requirements.
While ISO 9001 provides the foundation for quality management, IATF 16949 supplements this by focusing on the specific needs of automotive manufacturers and suppliers. It is aimed at improving quality, eliminating defects, and reducing waste throughout the supply chain.
Benefits of IATF 16949 Certification
-
Increased Customer Satisfaction: By meeting stringent quality requirements, businesses can ensure customer satisfaction and build long-term relationships. IATF 16949 certification demonstrates a commitment to delivering high-quality products.
-
Enhanced Product Quality: The standard focuses on reducing defects and improving product reliability, leading to enhanced product quality and consistency across the supply chain.
-
Compliance with Industry Requirements: Many automotive manufacturers require their suppliers to be certified to IATF 16949. Achieving certification opens doors to new business opportunities and ensures compliance with industry-specific regulations.
-
Streamlined Processes: Implementing IATF 16949 encourages a process-based approach, leading to more efficient and streamlined operations. This helps reduce costs, minimize waste, and improve overall performance.
-
Competitive Advantage: Certification provides a competitive edge by demonstrating your organizations commitment to quality and continual improvement. This can help you win contracts and expand your market share.
-
Risk Management: The standard emphasizes proactive risk management, ensuring that potential issues are identified and addressed before they affect product quality. This helps businesses prevent costly defects and recalls.
-
Global Recognition: IATF 16949 is recognized internationally, making it easier for businesses to compete in global markets. Certification can improve your reputation and credibility with customers, suppliers, and stakeholders.
Who Can Apply IATF 16949 Certification?
IATF 16949 certification is applicable to organizations involved in the automotive supply chain, including:
- Manufacturers: Companies that produce automotive components, parts, and systems, such as engine parts, transmission systems, electrical components, and more.
- Suppliers: Organizations that provide materials, components, or services to automotive manufacturers, including raw material suppliers, component manufacturers, and service providers.
- Service Providers: Companies offering services related to automotive manufacturing, such as engineering, testing, and maintenance.
- Consultants: Organizations that support automotive companies in implementing quality management systems and achieving certification.
- Aftermarket Parts Manufacturers: Companies that produce parts and accessories for vehicles after they have been sold, contributing to the maintenance and repair of automobiles.
- OEMs (Original Equipment Manufacturers): Manufacturers that produce vehicles and original components for vehicles.
How Can You Apply IATF 16949 Certification
-
Gap Analysis: Conduct a gap analysis to assess your current processes against the requirements of IATF 16949. This will help identify areas for improvement and guide the implementation process.
-
Develop a QMS: Create a Quality Management System (QMS) that meets the standards of IATF 16949. This system should cover all aspects of your operations, from product design and development to production and delivery.
-
Employee Training: Train employees on the requirements of the standard and their roles in maintaining quality. Employee engagement is key to the success of the QMS.
-
Internal Audits: Regularly conduct internal audits to ensure compliance with IATF 16949. This will help identify non-conformities and areas for improvement.
- External Audit and Certification: Undergo an external audit by an accredited certification body. Once your QMS is found to meet the requirements of IATF 16949, you will be awarded certification.
Why Choose Everest Consultrain for IATF 16949 Certification?
At Everest Consultrain, we specialize in helping automotive organizations achieve IATF 16949 certification. Our experienced team provides expert guidance throughout the certification process, from gap analysis to preparing for the final audit.
We understand the unique challenges faced by the automotive industry and tailor our services to meet your specific needs. With Everest Consultrain, you can be confident that your business will achieve certification efficiently and effectively.
Learn more about our ISO Certification Services and how we can help your organization succeed.
For more information on IATF 16949 and related standards, visit the International Automotive Task Force website.
Conclusion
Achieving IATF 16949 certification is essential for businesses in the automotive industry to ensure high-quality products, customer satisfaction, and compliance with industry standards. Partner with Everest Consultrain for expert support throughout the certification process and improve your competitiveness in the global market.
YouTube Video
For a deeper understanding of IATF 16949 and its significance, watch this informative video: